Entrevistamos a Gustavo Zúñiga Libano, subgerente de Producción en Botanical Solution
En RAYPA nos gusta saber de primera mano para qué usan nuestros clientes nuestros preparadores de medios de la Serie AE-MP. Solo así podemos mejorar, si cabe, nuestros equipos y nuestro servicio. Además, creemos que es la mejor manera de darte a conocer sus ventajas y todo lo que nuestros preparadores de medios pueden hacer en tu laboratorio.
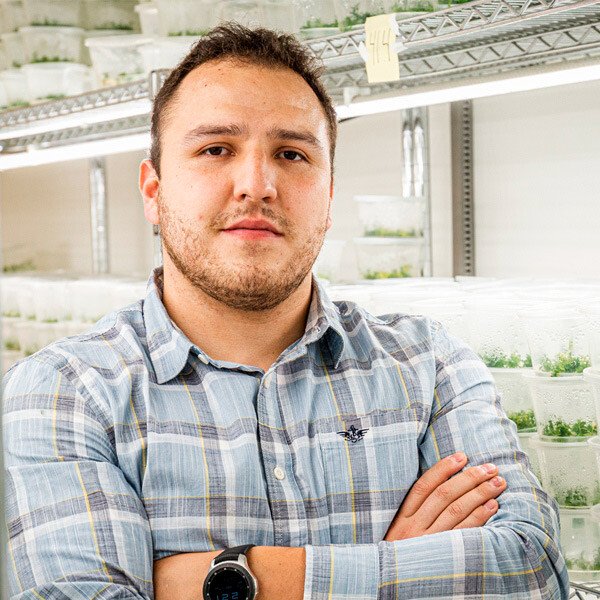
Por ello, en esta ocasión, entrevistamos a Gustavo Zúñiga Libano, Subgerente de Producción en Botanical Solution, además de ingeniero en biotecnología con experiencia en el diseño y operación de bioprocesos.
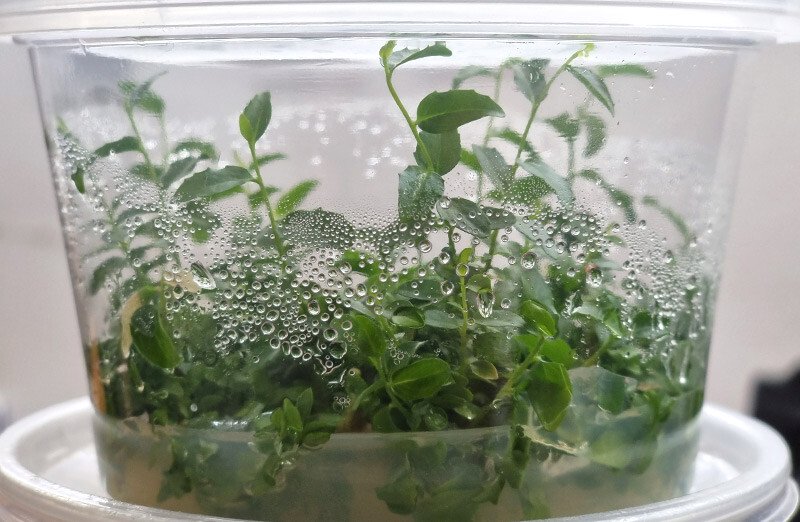
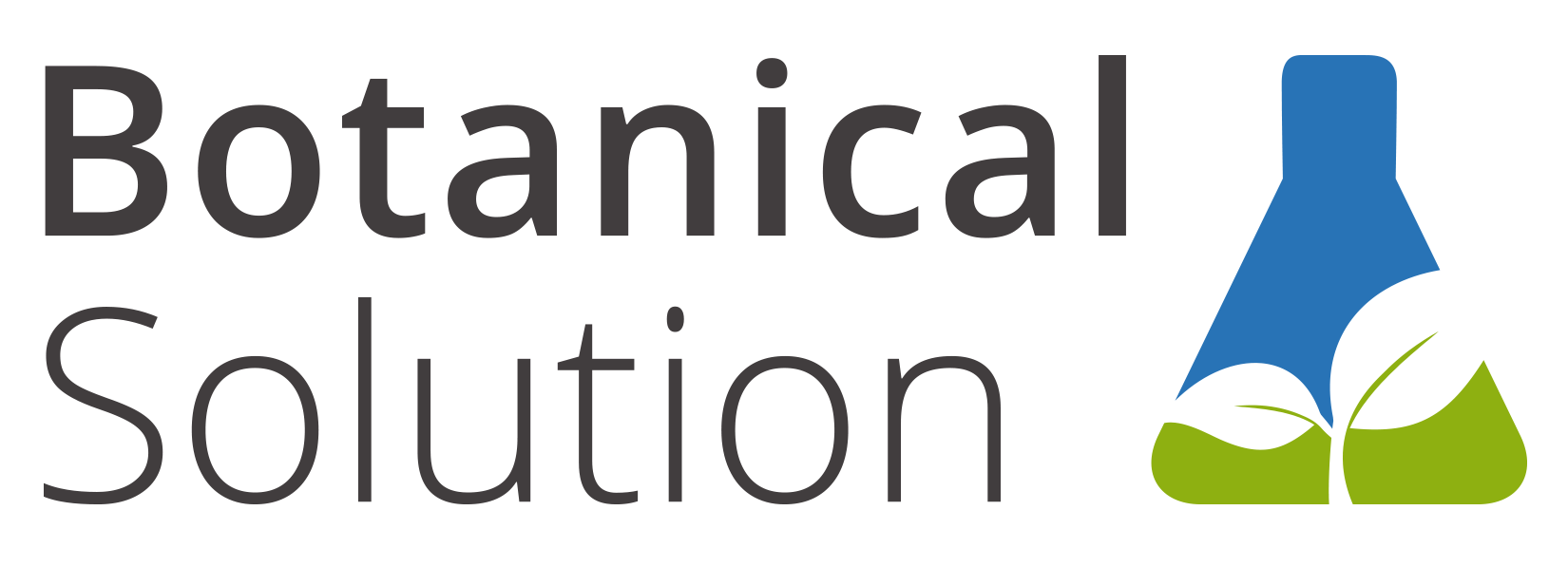
Botanical Solution es una compañía biotecnológica nacida en Chile cuyo propósito es mejorar la vida de las personas y del planeta a través del desarrollo de soluciones confiables, innovadoras y sustentables, que se basan en la ciencia y el aprendizaje de la naturaleza. Por ello, desarrollan productos para la protección de cultivos agrícolas y la salud humana, mediante la elaboración de materias primas avanzadas de origen botánico producidas por tecnologías propietarias de cultivo de tejidos vegetales.
Cuentan con dos grandes áreas de negocio. Una, en proceso de desarrollo, y que está relacionada con el ámbito farmacéutico. Y la otra, ya totalmente desarrollada, centrada en la industria agrícola y con convenios con multinacionales como Syngenta, que opera como distribuidor de su producto.
Además, sus productos producidos a partir del Quillay, una planta endémica de Chile, han sido altamente atractivos para la industria Agro y Farmacéutica, tanto en mercados nacionales como internacionales, siendo premiados como la mejor Startup biotecnológica de 2022 a nivel global por The World BioProtection Forum (WBF) y también han estado nominados dentro de las 25 “Soonicorns” chilenas por parte de MIC Innovations, entre otros importantes reconocimientos.
-
Antes de entrar en materia, Gustavo, ¿podrías darnos a conocer la historia de Botanical Solution?
Pues claro. A partir de un estudio desarrollado para la Universidad de Santiago de Chile en 2010 se descubrió que el Quillay o Quillaja saponaria, un árbol endémico de Chile, cultivado bajo ciertas condiciones producía unos compuestos que le conferían propiedades de biocontrol, especialmente al inicio de su desarrollo.
Dicha investigación era para obtener plantas con actividad biológica que pudieran tener algún impacto sobre el control del hongo Botrytis cinérea, el cual afecta a los cultivos de vid, ya que Chile es mundialmente conocido por la producción de uvas y de vinos, con una industria vinífera de las más grandes.
En 2017, tras los pertinentes procesos de registro de patentes y propiedad intelectual, nos establecimos formalmente como Botanical Solution para producir este árbol endémico mediante el cultivo in vitro. Por una parte, lo que hacemos es producir el Quillay a través del cultivo in vitro y biotecnología vegetal, para generar biomasa enriquecida con esos compuestos con actividad de biocontrol y que resultan de interés para el sector agrícola.
Esta biomasa tiene un metabolito que, en el caso agrícola, nos ha permitido registrar el producto en Perú y ahora también lo estamos registrando en México y Estados Unidos. Y próximamente en Europa y en Brasil. Para la industria agrícola lo que vendemos es un extracto de Quillay, un extracto con una concentración al 10% llamado Botristop® y que posee una actividad biológica fungicida diferenciadora del Quillay silvestre.
El 2020, con la pandemia, iniciamos nuestra segunda área de negocio, aún en desarrollo y basada en la producción de una saponina producida también por el Quillay y que se utiliza como adyuvante en vacunas. Es un ingrediente con demanda muy creciente para la producción de vacunas. A nivel de funcionamiento, básicamente este compuesto ayuda a potenciar la respuesta inmune de las personas.
La producción de esta saponina la realizamos por síntesis biológica que hace la misma planta de manera natural, pero que a través de las condiciones que le damos nosotros de medios de cultivo y de protocolos de crecimiento específicos podemos producir de forma eficiente y estandarizada, aspectos cruciales para poder proveer a clientes de la industria farmacéutica.
-
¿Por qué por cultivo in vitro y no por un método tradicional?
Lo hacemos mediante cultivo in vitro porque a través de las condiciones de crecimiento especificas podemos estandarizar la calidad de la producción a lo largo del tiempo. Nosotros utilizamos la planta como un vehículo para producir las moléculas que son de nuestro interés.
Otra importante razón por la que optar por el cultivo in vitro, y que liga con nuestra misión y visión, es por proteger el medio ambiente. Para producir una cantidad de biomasa equivalente a la que producimos actualmente vía el cultivo tradicional se requeriría un área de terreno importante, la tala de los árboles silvestres presentes en ese terreno, además de consumir más recursos hídricos y una mayor huella de carbono, por lo que el cultivo in vitro es mejor para el medio ambiente en todos los aspectos. Nuestra misión como compañía es proteger el bosque nativo de nuestro país.
Aunque el cultivo in vitro tiene la desventaja de que a lo largo de las generaciones se pueden perder ciertas propiedades, gracias a nuestro sistema de reintroducción de material a través de brotes, conseguimos mantener la producción estable.
En esencia, lo que en Botanical Solution producimos son plántulas que van en contenedores estériles, pero nuestro producto no termina en una planta desarrollada y con raíz que después se lleva a tierra, sino que una vez esta crece lo suficiente pasamos al proceso de cosecha y extracción de estos compuestos. Esa es la gran diferencia y ventaja de Botanical Solution.
“Gracias al preparador de medios hemos triplicado nuestra producción de plantas de Quillay”.
Gustavo Zúñiga Libano, Subgerente de Producción en Botanical Solution.
-
¿En qué momento decidisteis introducir el preparador de medios?
A raíz de los buenos resultados que os he contado y que nos permitieron la entrada en el sector farmacéutico, tuvimos que empezar a escalar nuestra parte productiva y, por eso, nos interesamos por vuestros preparadores de medios. Ahora contamos con el modelo de 100 litros, y gracias a él hemos podido triplicar nuestra producción de plantas de Quillay en nuestro laboratorio.
Parte del cuello de botella que teníamos era que la preparación de estos medios semisólidos se hacía de forma muy manual. Entonces teníamos que preparar por lotes el medio de cultivo utilizando autoclaves para esterilizar contenedores completos.
-
¿En qué momento el preparador de medios empieza a ser rentable respecto a la preparación manual?
El preparador de medios se hizo rentable a partir del año pasado, cuando estábamos proyectando en el mercado agrícola de Perú que también tiene una alta demanda en productos de este tipo y, por lo tanto, nuestra producción tenía que duplicarse o triplicarse. A partir de ahí, nos dimos cuenta de que una forma de hacer más eficiente la producción era eliminando esos cuellos de botella.
“La preparación de los medios de cultivo con el preparador de medios terminó siendo determinante porque nos ayudó a reducir la demanda de mano de obra a la mitad”.
Gustavo Zúñiga Libano, Subgerente de Producción en Botanical Solution.
-
A nivel operativo, ¿cuánto personal está implicado en el cultivo de tejidos vegetales?
Yo tengo 67 personas a mi cargo, repartidas en 2 turnos, de día y de noche. Y en la parte productiva de plantas tenemos alrededor de 40 personas. Es un proceso que por la tecnología es manual, todavía no hay automatización del corte de planta, pero por lo mismo buscamos formas de hacer más eficiente toda la productividad en otras áreas.
La preparación de los medios de cultivo con el preparador de medios terminó siendo determinante porque nos ayudó a reducir la demanda de mano de obra a la mitad. En un principio, teníamos proyectado que para la producción de medios manual necesitábamos un equipo de 8 a 10 personas. En cambio, al introducir vuestro preparador de medios esto cambió y, hoy día, tenemos por cada turno un equipo de 3 personas y producimos una mayor cantidad.
En la actualidad, nos alcanza con el preparador de medios que tenemos, pero si seguimos creciendo, como parece que haremos, necesitaremos otro equipo de refuerzo.
-
¿Cómo conocisteis el preparador de medios de RAYPA?
Lo conocimos investigando. En 2018, cuando recién nos estábamos instalando, yo contacté con Marc Perez, el responsable de LATAM en RAYPA, el cual nos dio a conocer el equipo y sus prestaciones. Pero como empresa que estaba creciendo nos vimos obligados a estudiar nuestras posibilidades económicas y priorizar. Pasado un tiempo, retomamos la idea y contactamos de nuevo con Marc y este nos trasladó con Farmalatina, que es la empresa distribuidora en Chile, y finalmente nos hicimos con el equipo.
Yo he trabajado en diferentes laboratorios de Europa, en Barcelona, pero en Chile no hay mucha difusión de este tipo de aparatos porque la industria no es tan grande.
-
¿Qué tal funcionó la puesta en marcha?
Pues la puesta en marcha funcionó bien por 2 razones. Primera, porque ya teníamos la experiencia de preparar medios de cultivo y no partíamos de cero. Y, segunda, porque es un equipo muy amigable, muy intuitivo por lo que desde el primer día que lo instalamos lo empezamos a utilizar.
Pienso que el preparador de medios de RAYPA cumple con unas condiciones que a veces no son tan normales en la industria de los laboratorios porque, por lo general, todo tiene mucha sofisticación y si bien este equipo es bastante sofisticado también es muy amigable con el usuario. Los operadores de máquinas que nosotros teníamos para otro tipo de autoclaves pudieron operar el equipo sin ningún problema.
-
A nivel de postventa, ¿habéis experimentado algún problema?
Cuando estuvo Marc en nuestro laboratorio lo que me comentó nuestra supervisora es que la manguera que alimenta la bomba peristáltica es de un material susceptible al uso, pero él nos dijo que es una pieza fácil de remplazar y que era sencillo enviárnosla desde España. Son pequeñas cosas que al poder comentarlas directamente nos dejan más tranquilos. Ese ha sido el único elemento que, en su momento, sí que nos preocupó, pero aún no nos ha fallado.
-
¿Alguna sugerencia?
Dentro de las automatizaciones que uno busca es tener en el preparador de medios una línea dosificadora. Entendemos que no es el foco de RAYPA, pero pensamos que para la compañía podría ser interesante avanzar en un kit de entrega automática del medio. Todos buscamos reducir y minimizar la cantidad de horas-hombre que esa labor implica. Por lo que sería muy interesante tener un equipo adicional que permita dosificar en línea.
Contamos con el dosificador automático de RAYPA que viene con el sensor, pero, de todos modos, tiene que haber un operario manejando los contenedores estériles e ir dosificando, por lo que el equipo no es completamente independiente.
-
¿Alguna otra cosa más que añadir, Gustavo?
Poco más que añadir porque la verdad es que estamos muy contentos. Nuestra experiencia con RAYPA ha sido muy buena, el soporte que nos ha dado Alejandro Sev de Farmalatina también ha sido muy satisfactorio.
- Desde RAYPA, queremos expresar nuestro agradecimiento, Gustavo, por haber dedicado una parte de tu tiempo para participar en esta entrevista. Ha sido un privilegio conocer de cerca tu experiencia con nuestros preparadores de medios. Tu historia servirá sin duda como fuente de inspiración para otros laboratorios de cultivo de tejidos vegetales.