We interviewed William Benoist, Owner of Plant & Palm Lab Biotechnologies.
Showcasing how our clients leverage our AE-MP Series media preparators is the best way to demonstrate the versatility and value of our products.
This time, we had the opportunity to interview William Benoist, the visionary owner of Plant & Palm Lab Biotechnologies (PPLB), headquartered in France. The company has established a global presence, particularly in Arab countries like Libya, Egypt, and Saudi Arabia, developing innovative plant biotechnology solutions.
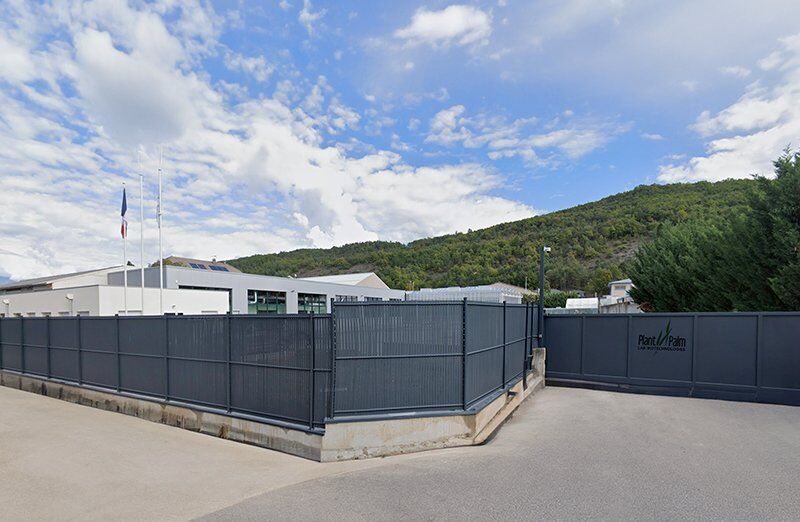
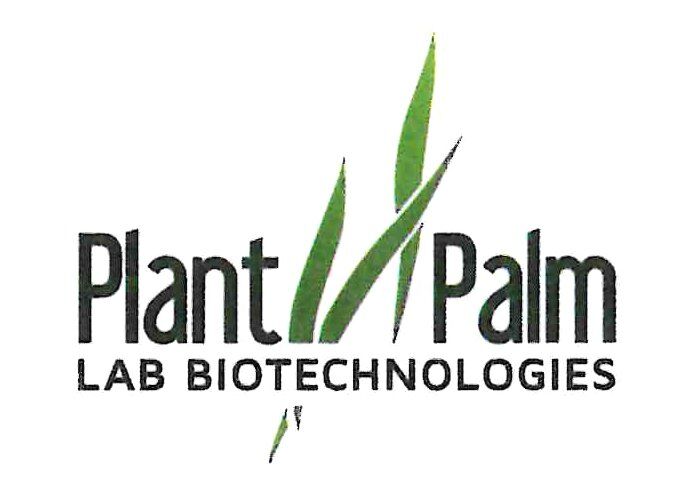
Plant & Palm Lab Biotechnologies (PPLB) is a plant biotechnology laboratory focused on covering various areas of research, including plant tissue culture. One of the lab’s main research projects is the application of tissue culture techniques for the in vitro propagation of date palms.
-
William, thank you for joining us today. Could you begin by telling us about the history of PPLB?
Certainly. The first company we founded in 2001 was called SerBiotech. After two decades, we decided to build our current lab, where we have been since September 2022. For that, we had to rely on foreign investors because it was an investment of nearly 4 million euros. They were clients we had been working with in Egypt, who had been wanting to collaborate with us for many years.
We provided the technology, and they provided the financing. This took place on January 1, 2021, and we transitioned from SerBiotech to PPLB. The French team retained 51% of the company, and the two Egyptian brothers, our partners, took the rest.
-
For those who may not be familiar with your work, could you explain PPLB’s focus in the field of plant biotechnology?
We are a laboratory specialized in the in vitro cultivation of plant tissues. My wife, Catherine, is the scientific director of the lab. She developed the technology based on organogenesis. We work with several plant species, but the one that offers the highest added value, and is the lab’s flagship product for which we are known worldwide, is the date palm.
We focus on reproducing date palms by multiplying thousands or even millions of plants that are genetically identical to the mother plant, without genetic drift. This is our main activity, recognized worldwide across the entire subtropical belt, from Mauritania to Indonesia, in about fifty countries where date palms are found and produce dates.
-
In which country is the company's main lab located, where all this production takes place?
Our main lab is located in France. We export our products weekly, ensuring they are clearly labeled with the ‘Made in France’ mark.
-
How many people are currently employed at PPLB, and do you have plans to expand?
At present, we have 20 technicians working between the lab and the acclimatization room. We plan to hire an additional 10 technicians in 2024 and 2025, bringing our team to around 30. This will allow us to increase our annual production capacity to 200,000-250,000 plants.
-
From what you've said, it seems you are planning to continue growing...
Absolutely. The annual demand ranges between eight and ten million plants, and we are currently among the top three producers worldwide. This shows that there’s still significant room for growth.
-
As you mentioned before we started the interview, PPLB is working on two projects. Where are they taking place, and what stage are they in?
Indeed, we are developing two projects, although they are taking time to materialize because they are in countries where it is difficult to work, such as Libya, Egypt, and Saudi Arabia. These are very complex countries, so we have to take things slowly, but it is something that will undoubtedly happen. We also have a project in Dubai, in the United Arab Emirates.
We have been working in all these countries for 25 years, and we are very well-known, which opens up many opportunities for collaboration.
-
Could you share the philosophy behind these projects?
Our philosophy is to ensure food security for the Muslim world and, for the past few years, to regulate the ecosystem, as a palm grove is much like the Amazon rainforest.
I’ll give you an example: when the Americans went to Iraq in 2003, they destroyed 50 million palm trees in two weeks. Twenty years later, that is, today, the temperature of that ecosystem has risen by 7.7 degrees. So, we need to replant palm trees to restore the ecosystem, for the sake of the climate.
So, there you have it, our objective is based on two very important systems for the planet: food security and climate regulation.
-
Let's focus on your work in the lab... When you first started, did you prepare culture media in autoclaves and flasks, or did you begin your work with a media preparator?
For ten years, we were a research and development lab. It was a bit like a back kitchen, very artisanal, a very small setup. We sold and produced enough plants to balance the structure, but we were in the process of preparing for the transition to industrial production.
Since 2021, we’ve shifted to industrial production and we equipped our lab with RAYPA technology, including a media preparator and multiple autoclaves.
-
Do you prepare different types of media or always the same type?
We always use the same type of base with agar-agar, although the chemical formulations vary depending on the varieties you’re feeding.
-
How did you come across our AE-MP Series media preparators?
My wife did her PhD at INRA (National Institute of Agronomic Research – Institut National de la Recherche Agronomique) with Alain Poupet in Antibes, where they were very familiar with the system. She gave me some brands, including RAYPA. I sent a message through the contact form, and someone from your company responded, telling me to get in touch with their distributor in France.
We got along very well with your distributor. The service was excellent in every way. They showed me that RAYPA equipment is state-of-the-art, user-friendly, with low maintenance costs and unmatched reliability.
From that point, I took responsibility for setting up the lab and procuring all the essential equipment, including autoclaves, laminar flow hoods, a media preparator, and an automatic dispenser.
-
How has the media preparator performed in your lab?
Well, it’s working fine, but it’s not yet operating at full capacity because we don’t work with Petri dishes but with tubes and jars, and it’s very complicated to dispense automatically with tubes, especially since we have tubes of different heights.
So, we use the media preparator and dispense manually, but with a four-outlet dispenser to fill four tubes at once. We save a lot of time, and above all, with the media preparator, the media is very stable and homogeneous.
We’re still not at 100% because we need to hire ten more employees before we can operate at full capacity. But right now, we’re producing about 50 liters daily.
-
What do you consider the most valuable features of the media preparator?
The autoclave door system is particularly impressive. When you have 20 different people using the equipment, they often don’t treat it properly… but with this equipment, things go well. Catherine had autoclaves which would break down every six months because of the door. She told me to find a door that worked well. Your distributor gave me a technical demonstration showing that there were no issues with your equipment.
So, aside from the laminar flow hoods, magnetic stirrers, and the things you don’t produce, practically all the equipment in the lab is yours: autoclaves, media preparators, ovens, etc. And, to this day, we are completely satisfied. We have your distributor nearby, which is great because they are the real link between us, and everything runs smoothly. We are delighted.
-
In your opinion, at what point does investing in a media preparator become profitable?
In my opinion, the purchase is mainly justified by the need to produce culture media in significant volumes. If the demand is below 10 liters a day, the investment isn’t worthwhile. However, if it exceeds 10 liters a day, it’s worth considering. There may be a gray area between 10 and 20 liters, but above 20 liters, there’s no doubt, a media preparator becomes essential for efficiency and productivity. Without it, too much time is wasted, and a technician would need to be fully dedicated to the task.
At PPLB, our technicians can focus on production. To ensure this, we rotate them through micro-teams, where they take turns preparing the media. This allows everyone to gain horizontal knowledge and be capable of working in all positions. So, for any structure, it really comes down to volume: below 10 liters, it’s unnecessary; between 10 and 20 liters, it’s worth considering; and above 20 liters, it becomes indispensable.
“Above 20 liters, there’s no doubt, a media preparator becomes essential for efficiency and productivity. Without it, too much time is wasted, and a technician would need to be fully dedicated to the task.”
William Benoist, Owner of Plant & Palm Lab Biotechnologies (PPLB)
-
Can you share your experience with RAYPA’s after-sales service?
I want to emphasize that without the outstanding work of your distributor, we wouldn’t have RAYPA equipment—it’s that simple. The reason we chose RAYPA is due to the highly professional support they provide. I have an excellent relationship with them; we communicate regularly, even when there are no issues. They call to check if everything is going smoothly, if there are any concerns, or if Catherine is encountering any difficulties in the lab. It’s a simple gesture, but it’s very reassuring.
We had an issue with a sensor in the media preparator during the first three months, while we were still in the testing phase. One of the sensors broke, and I’m not exactly sure why. It was fixed in three or four days. Your distributor immediately called you, got in touch with the after-sales service team, and they sent the part. Three days later, it was here, installed, and the problem was resolved.
This is crucial because a lab like ours, currently one of the leading plant biotechnology labs in Europe, cannot be out of service for three days. If we don’t prepare media for three days, we won’t produce for three days. The lab has to keep running.
-
What do you value most about RAYPA?
Aside from the high quality of your autoclaves and media preparators, I value the ability to maintain a relationship with the customer, beyond just selling a machine.
At PPLB, we work with date palms, which have a very long growth cycle, so longevity is about loyalty and commitment. And when you are loyal to a company like RAYPA, it’s a matter of symbiosis. The relationship continues, and so does the equipment.
For the next lab I equip, I will call your distributor directly and say, ‘Look, I need this.’ Then, I might do a quick price check, but other than that, the trust is there—in the equipment, in the quality, and in the service. So, we keep moving forward, and neither of us wastes time.
“Aside from the high quality of your autoclaves and media preparators, I value the ability to maintain a relationship with the customer, beyond just selling a machine.”
William Benoist, Owner of Plant & Palm Lab Biotechnologies (PPLB)
-
Are there any improvements you would suggest for RAYPA’s media preparators?
Today, we have a year of hindsight because, during the first three or four months, we were in the testing phase. So, we can’t really base things on that period. We have 2023 and half of 2024 to reflect on. It would be dishonest for me to say there has been a negative point because I don’t know of any. My wife works in the lab every day and has never made any negative comments about using the equipment.
On the other hand, regarding the automatic media dispenser that connects to the preparation unit, I think it would be a good idea for your R&D lab to study the possibility of dispensing into tubes with a more ‘fluid’ system, which would save us from needing more technicians for that task.
Currently, automatic dispensing into tubes is an area that doesn’t work properly. If RAYPA ever develops an automatic dispenser for tubes with a 2.5 diameter that meets our needs, we would be interested in testing it to see if we can free up a technician from that task.
We have tubes that are 20 and 25 in height, and all have a 2.5 diameter. So, they are placed in racks. We would need to find racks that fit the dispenser, allowing the tubes to be placed correctly, along with a dispensing arm system. But that’s something for research and development. Over time, we’d like to be able to automate it, making the process fully robotic.
- Thank you, William, for sharing your insights and the journey of PPLB. Your experience will undoubtedly inspire other biotechnology companies to explore RAYPA’s solutions.