We interviewed Gustavo Zúñiga Libano, Assistant Production Manager at Botanical Solution
At RAYPA, we like to know firsthand how our customers are using our AE-MP Series media preparators. That way, we can further improve our equipment and our service. In addition, we believe that it is the best way to let you know its advantages and everything that our media preparators can do for your laboratory.
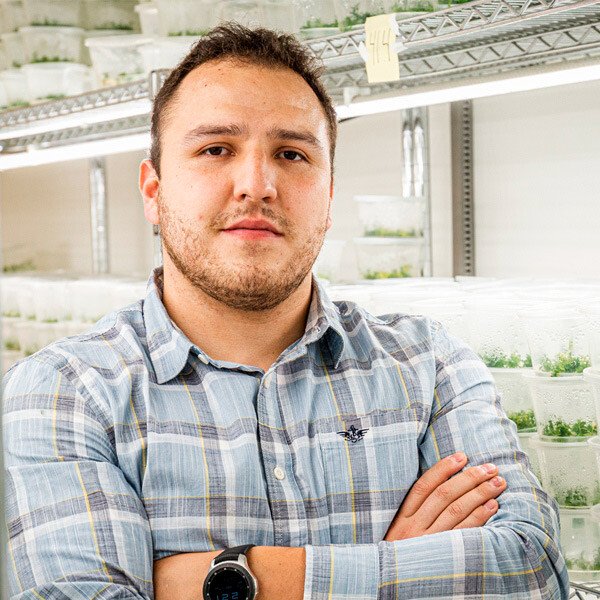
For this reason, on this occasion, we interviewed Gustavo Zúñiga Libano, Assistant Production Manager at Botanical Solution, as well as a biotechnology engineer with experience in the design and operation of bioprocesses.
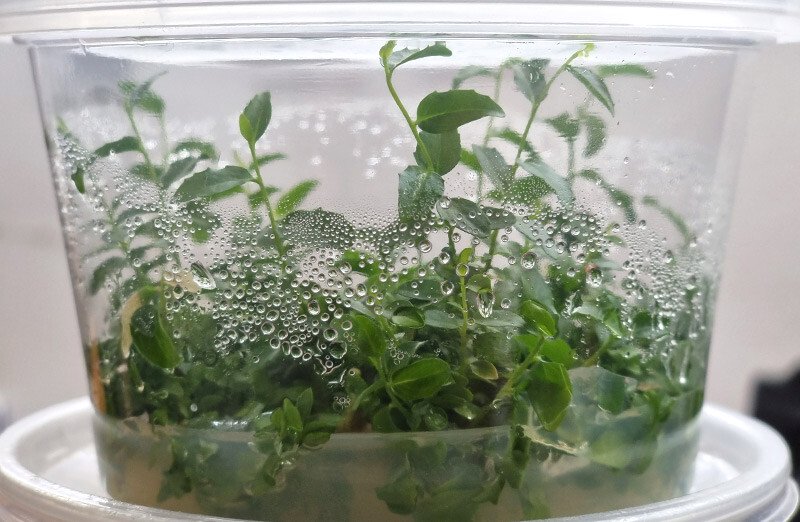
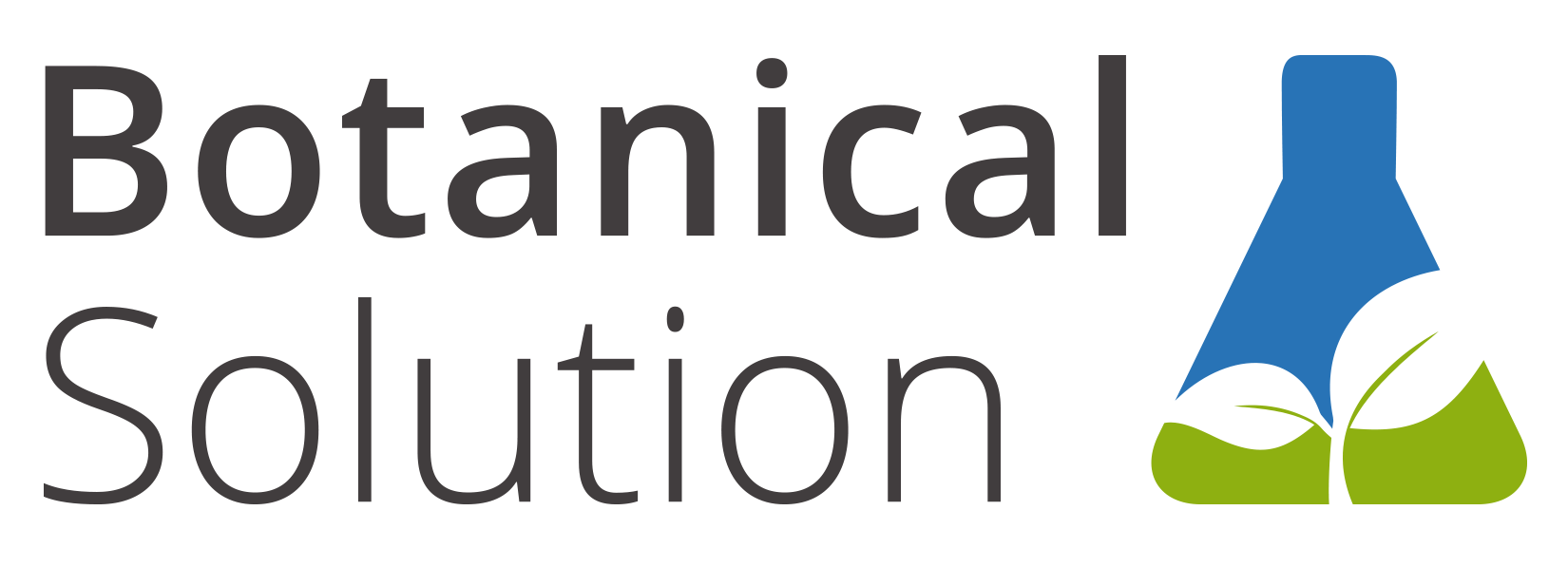
Botanical Solution is a biotechnology company born in Chile whose purpose is to improve the lives of people and the planet through the development of reliable, innovative and sustainable solutions, based on science and learning from nature. Therefore, they develop products for the protection of agricultural crops and human health by developing advanced botanical-based raw materials produced by proprietary plant tissue culture technologies.
They have two main business areas. One, currently in development, is related to the pharmaceutical field. And the other, already fully developed, is focused on the agricultural industry and has agreements with multinationals such as Syngenta, which operates as a distributor of its product.
In addition, its products produced from Quillay, an endemic plant of Chile, have been highly attractive to the Agro and Pharmaceutical industry, both in national and international markets, being awarded as the best biotech Startup of 2022 globally by The World BioProtection Forum (WBF), and have also been nominated among the top 25 Chilean “Soonicorns” by MIC Innovations, among other important recognitions.
-
Before going into detail, Gustavo, could you give us an overview of Botanical Solution's history?
Of course. From a study developed for the University of Santiago de Chile in 2010, it was discovered that the Quillay or Quillaja saponaria, an endemic tree of Chile, cultivated under certain conditions, produced compounds that conferred biocontrol properties, especially in the early stages of its development.
This research aimed to obtain plants with biological activity that could have some impact on the control of the fungus. Botrytis cinerea, which affects vine crops, since Chile is known worldwide for the production of grapes and wines, with one of the largest wine industry.
In 2017, after completing the necessary patent and intellectual property registration processes, we formally established ourselves as Botanical Solution to produce this endemic tree through in vitro culture. On the one hand, what we do is produce Quillay through in vitro culture and plant biotechnology to generate biomass enriched with those compounds that have biocontrol activity and are of interest to the agricultural sector.
This biomass has a metabolite that, in the agricultural case, has allowed us to register the product in Peru and now we are also registering it in Mexico and the United States. And soon in Europe and Brazil. For the agricultural industry, what we sell is a 10% concentrated extract of Quillay called Botristop®, which has a biological fungicidal activity that differentiates it from wild Quillay.
In 2020, with the pandemic, we started our second business area, still under development and based on the production of a saponin also produced by Quillay and used as an adjuvant in vaccines. It is an ingredient with a rapidly growing demand for vaccine production. In terms of functionality, this compound essentially helps enhance the immune response in individuals.
We produce this saponin through biological synthesis that the plant itself naturally performs. However, by providing specific culture media and growth protocols, we can produce it in an efficient and standarized way, which are crucial aspects for supplying pharmaceutical industry clients.
-
Why choose in vitro culture and not a traditional method?
We do it through in vitro culture because by implementing specific growth conditions, we can standardize the quality of the production over time. We use the plant as a vehicle to produce the molecules that are of interest to us.
Another important reason to opt for in vitro culture, which aligns with our mission and vision, is to protect the environment. To produce an equivalent amount of biomass to what we currently produce through traditional cultivation would require a significant area of land, the felling of the wild trees present on that land, in addition to consuming more water resources and a larger carbon footprint. Therefore, in vitro culture is better for the environment in all aspects. Our company’s mission is to protect the native forest of our country.
Although in vitro cultivation has the disadvantage of potentially losing certain properties over generations, our system of reintroducing material through shoots allows us to maintain stable production.
Essentially, what we produce at Botanical Solution are seedlings that come in sterile containers. However, our product doesn’t end with a fully developed and rooted plant that is later transplanted into the ground. Instead, once the plant has grown sufficiently, we proceed to the harvest and extraction process of these compounds. That is the significant difference and advantage of Botanical Solution.
“Thanks to the media preparator we have tripled our production of Quillay plants.”
Gustavo Zúñiga Libano, Assistant Production Manager at Botanical Solution.
-
At what point did you decide to introduce the media preparator?
As a result of the positive results I mentioned earlier, which allowed us to enter the pharmaceutical sector, we had to start scaling up our production. That’s why we became interested in your media preparators. We now have the 100-litre model, and thanks to it we have been able to triple our Quillay plant production in our laboratory.
Part of the bottleneck we had was that the preparation of these semi-solid media was done in a very manual way. We had to prepare the culture media in batches using autoclaves to sterilize entire containers.
-
At what point does the media preparator start to become cost-effective compared to manual preparation?
The media preparator became profitable last year, when we were were targeting the agricultural market in Peru, which also has a high demand for products of this type and, therefore, our production had to be doubled or tripled. From that point on, we realized that one way to make production more efficient was by eliminating those bottlenecks.
“The preparation of the culture media with the media preparator ended up being decisive because it helped us to reduce the demand for human labor in half.”
Gustavo Zúñiga Libano, Assistant Production Manager at Botanical Solution.
-
At an operational level, how many personnel are involved in plant tissue culture?
I have 67 people under my responsibility, divided into two shifts, day and night. And in the plant production department, we have around 40 people. It is a process that, due to the technology involved, is still manual. There is currently no automation for plant cutting. However, because of this, we are seeking ways to make the entire productivity more efficient in other areas.
The preparation of the culture media with the media preparator ended up being decisive because it helped us to reduce the demand for human labor in half. Initially, we projected that we would need a team of 8 to 10 people for manual media production. However, with the introduction of your media preparator, this changed, and now we have a team of 3 people per shift and we produce a greater quantity.
Currently, the media preparator we have is enough for us, but if we continue to grow, as it looks like we will, we’ll need another unit.
-
How did you find out about RAYPA media preparator?
We discovered it through research. In 2018, when we were just getting set up, I contacted Marc Perez, the LATAM manager at RAYPA, who introduced us to the equipment and its features. However, as a growing company, we were forced to assess our economic possibilities and prioritize accordingly. After a while, we resumed the idea and contacted Marc again and he transferred us to Farmalatina, which is RAYPA’s distribution company in Chile, and we finally got the machine.
I have worked in different laboratories in Europe, in Barcelona, but in Chile, there is not much awareness of this type of equipment because the industry is not as large.
-
How was the experience with the equipment start-up process?
Well, the start-up worked well for 2 reasons. First, because we already had experience in preparing culture media and we were not starting from scratch. And, secondly, because it is a very user-friendly and intuitive equipment, so we started using it from the first day we installed it.
I believe that RAYPA media preparator meets certain conditions that are not always common in the laboratory industry because, in general, everything is highly sophisticated. While this equipment is indeed quite sophisticated, it is also very user-friendly. The machine operators we had for other types of autoclaves were able to operate the equipment without any issue.
-
At the after-sales level, have you experienced any problems?
When Marc visited our laboratory, our supervisor mentioned that the hose that feeds the peristaltic pump is made of a material that is susceptible to wear. However, he assured us that it is an easily replaceable part and can be sent to us from Spain without difficulty. These are small issues that, when discussed directly, leave us more at ease. That has been the only element that, at the time, did concern us, but it has not failed us yet.
-
Do you have any suggestions?
One suggestion would be to incorporate a dosing line into the media preparator as part of the automation features. We understand that it may not be the primary focus of RAYPA, but we believe that it could be interesting for the company to explore the development of an automated media delivery kit. We all seek to reduce and minimize the number of man-hours involved. So it would be highly interesting to have an additional equipment that enables in-line dosing.
We have RAYPA external dosing station that comes with a sensor, but regardless, an operator still needs to handle the sterile containers and perform the dosing manually. Therefore, the equipment is not entirely independent.
-
Anything else to add, Gustavo?
There is little else to add because, truthfully, we are very satisfied. Our experience with RAYPA has been very positive, and the support provided by Alejandro Sev from Farmalatina has also been highly satisfactory.
- From RAYPA, we want to express our gratitude, Gustavo, for having dedicated part of your time to participate in this interview. It has been a privilege to learn about your experience with our media preparators. Your story will undoubtedly serve as a source of inspiration for other plant tissue culture laboratories.